Blog and News
Is it Necessary to Measure Environmental Conditions in Resinous Flooring Installations?
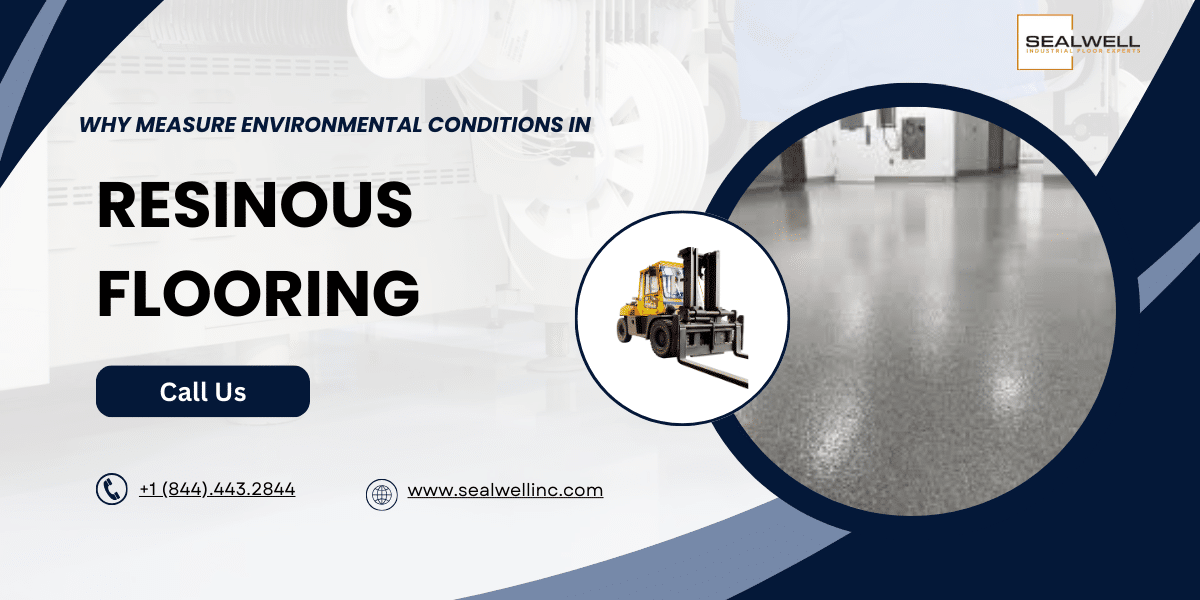
In industrial and commercial settings, resinous flooring options like epoxy and polyurethane, are highly preferred for their durability, chemical resistance, and ease of maintenance. Their incredible property to create seamless, long-lasting surfaces and ability to withstand heavy traffic make them ideal for warehouses, manufacturing units, and other busy environments.
Despite these compelling benefits, many businesses fail to achieve the desired shine and strength due to improper environmental conditions during flooring installation.
Are you facing the same hurdle? It’s because you haven’t measured or controlled the key environmental factors like temperature, humidity, and dew point during the installation process.
Why Environmental Conditions Matter in Resinous Flooring Installations
Resinous flooring materials including epoxy and polyurethane undergo a precise chemical curing process to offer better strength and resilience. This process is, indeed, very sensitive to environmental factors such as temperature, humidity, and substrate moisture levels. Failing to maintain and control these aspects during floor installation thus leads to the following issues.
- Poor Adhesion: To build an effective bond between the resinous flooring material and the existing substrate, the surface area must be clean, dry, and thoroughly prepared. Remember, excessive moisture on the floor or high humidity can restrict the resin from adhering properly. It leads to de-lamination or bubbling over time.
- Incomplete Curing: Do you know each resinous flooring system has specific environmental requirements to cure properly? For example, with very low temperatures, the curing process slows down, leaving the floor weak. In contrast, high temperatures accelerate curing, making it difficult to achieve a smoother finish. It’s important to understand them before initiating the process.
- Surface Defects: Poor environmental conditions can lead to surface imperfections. These include bubbling, cracking, blushing, fish eyes, peeling, etc.
- Reduced Resistance: Improper environmental control leads to incomplete curing which further affects the development of strength and chemical resistance. This reduces the floor’s longevity and simultaneously increases maintenance costs.
Key Environmental Conditions to Measure
To prevent the above-mentioned issues, it’s necessary to keep track of the following conditions. Let’s get a detailed insight into them.
Temperature
Ideal ambient temperature range: 10°C to 30°C (50°F to 86°F).
The substrate temperature should be at least 3°C (5°F) above the dew point to avoid condensation.
Humidity
Relative humidity (RH) should be below 75% for most resinous systems.
High humidity can lead to poor curing and surface blushing.
Dew Point
The dew point must be monitored to avoid condensation, which can weaken the bond between the resin and the substrate.
Substrate Moisture Level
Use a moisture meter to ensure the substrate moisture level meets the product’s specifications (typically below 5%).
Excessive moisture can cause bubbling and poor adhesion.
Understanding Resinous Flooring Systems
To set up a safe, durable, and effective flooring system in your industrial or commercial space, it’s crucial to understand how they respond to environmental factors.
Epoxy Coatings
- Optimal Substrate Temperature: Ensure the substrate temperature remains between 10°C and 30°C (50°F to 86°F) for proper curing.
- Maintain Ideal Humidity Levels: Keep relative humidity below 85% during the application process to avoid curing problems.
- Condensation Checks: If the substrate temperature drops below the dew point, condensation can form, leading to poor adhesion and a cloudy finish.
- Direct Cooling: Air conditioning or direct cooling can create moisture buildup on the surface, causing defects.
- Best Practice: Keep the substrate temperature at least 3°C (5°F) above the dew point to avoid condensation-related problems.
Polyurethane Coatings
- Optimal Substrate Temperature: Maintain between 5°C to 30°C (41°F to 86°F) for optimal performance.
- Potential Risks: Low temperatures can delay curing, while high temperatures can accelerate it, making the material harder to work with.
- Direct Cooling: Sudden cooling in high-humidity environments can interfere with the curing process.
- Best Practice: Use heaters or dehumidifiers to keep temperature and humidity levels stable.
Best Practices for a Successful Flooring Installation
- Measure temperatures accurately in advance.
- Control the environment
- Plan for seasonal changes
- Follow manufacturer guidelines
The Bottom Line
Maintaining the temperature, dew point, and humidity of the environment is essential for a flawless flooring installation. However, without professional guidance, it’s hard to ensure whether the surface area is ready for transformation. That’s when Sealwell appears!
Our skilled and trained installers follow the industry guidelines and embrace the best practices to prevent common issues. This ultimately maximizes the quality and lifespan of resinous flooring. Give us a call and schedule a free consultation today.
SEALWELL INC
Phone No– +1 (844)-443-2844
Email- in*******@se*********.com
Let’s Connect: www.sealwellinc.com
Address- 11660 Alpharetta Hwy, Suite 105, Roswell, GA 30076, United States